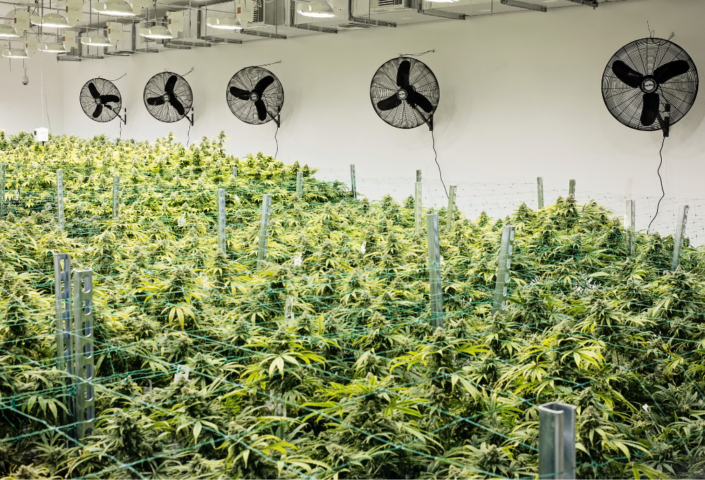
The Importance of Inventory Observations
For cannabis companies that require audited financial statements that conform with Generally Accepted Accounting Principles (GAAP), an auditor must observe their year-end inventory. Whether cannabis companies are retail dispensaries or cultivation and extraction facilities, inventory counts are critical; they are called ‘material’ and are part of the balance sheet.
Inventory observation requirements started in the late 1970s when there were several well-publicized large-scale fraud cases. In one case, MiniScribe, a Longmont, Colorado manufacturer of disk storage products, packed bricks in shipping boxes to pass them off as hard drive inventory ready to be sold. An inventory observation would have uncovered this financial fraud.
Today, more and more cannabis companies have their financial statements audited for a variety of reasons. Some states require audited financial statements as part of an operator’s license renewal process. Other cannabis companies use audited financial statements as due diligence for a company sale or merger. Some cannabis companies find audited financials lower their cost of capital when raising or borrowing money.
In preparation for inventory observations that I perform on Bridge West’s clients, I visit clients within a day or two of year-end. The goal is to determine if we can rely on the accuracy of the inventory counts in the reports. I take test counts and compare them to the inventory reports from their cannabis software. The next step is to use the reports to price the individual line items, at cost. Then, we calculate the total value of the inventory on the company’s balance sheet.
To perform a recent inventory observation, I visited a client that recently acquired a retail dispensary and a large cultivation site. I met with the Head of Inventory and their General Manager (GM), who provided some insights. They said that the pound bags ‘fly off the shelves’ in a matter of days; however, this is not the case for the other cannabis products like edibles, tinctures, concentrates, and capsules. While these products constitute half of the store’s sales, slow-moving products can sit for months and then must be properly disposed of, as they near their expiration dates. The GM and I counted these items, including large see-through plastic bags that held pre-rolled one-gram joints, and one-pound bags of very high-quality marijuana. All the bags matched the grams noted on the inventory report. At most dispensaries, a high percentage of the value is in the pounds of marijuana, usually stored in one-pound bags in a locked room or large safe.
Then we headed to tour their cannabis cultivation facility that houses over 10,000 plants. The cultivation center included tiny clones that were four inches high, mature plants, and six-foot-high ‘mother plants.’ They are called ‘mother plants’ because cuttings are taken from them to become clones. A facility like this can produce thousands of pounds a year, although yields vary greatly depending on the strain.
This client’s cultivation facility had very accurate plant counts that matched the Metric reports. Their plants looked very healthy and showed no signs of yellow leaves to indicate they were afflicted with any plant diseases that can lead to the destruction of the entire grow room.
As background, the State of Colorado’s tracking system is called Metric. The theory behind Metric is that every gram of cannabis is tracked from the time the clone goes into the bucket of soil until it is sold to the customer, in the case of recreational marijuana, or to the patient, in the case of medical marijuana. The State of Colorado’s regulatory agency is The Marijuana Enforcement Division (The MED) that established several goals for the Metric System, including:
- Preventing out-of-State shipments of cannabis
- Preventing sales to minors
- Ensuring the State collects its proper taxes
- Tracking products that make people sick to recall them
For cannabis companies, this process is a lot of work. Plants are marked with inventory tags that track them from baby clones through to mature plants that are harvested, dried, and packaged in one-pound bags. Shipments of the bags are tracked from the cultivator to the dispensary. Packaged ounces, quarter and eighth ounces, and joints, are labeled with their batch numbers and harvest dates. When the bags arrive at retail locations, they are immediately logged into the stores’ Metric system. They are then packaged into individual plastic containers by weight with the labels attached.
For cannabis employees, this is a continuous process throughout the day. Deliveries can happen anytime the store is open. At most large cannabis companies, a Head of Inventory and the Store Managers work together to oversee this process and root-out exceptions.
During my inventory observation visit, I was pleased that our client had very accurate inventory numbers and my test counts were exact to the Metric reports. Overall, my trip was a success!
If you have any questions about inventory observation requirements, or would like to discuss how inventory tracking and observations can impact your business, please contact Jim Marty, CEO and Founder of Bridge West at jmarty@bridgewestcpas.com.